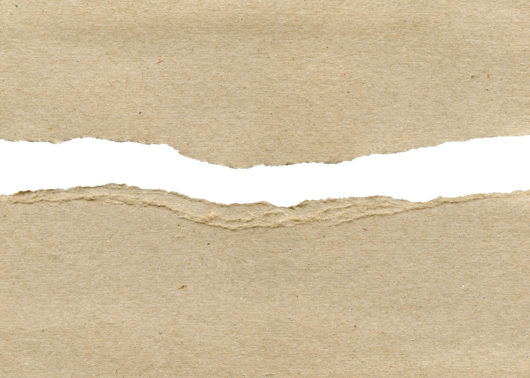
We know a few things from experience: you can’t unbreak someone’s heart, and you can’t regain the productivity lost from a paper break in your facility.
But broken hearts mend, and once the aftermath of your paper break has been cleaned up and contained, there are solid ways to prevent it from happening again.
A costly and time-consuming mess
Picture this: you’ve been hard at work all day helping your plant produce gypsum wallboard. Just when you find five minutes to grab a cup of coffee, the horn blows long and hard, signaling a shutdown of the board line.
The line is down, and you’ve got to drop everything to help clean it up. It usually takes about 20 minutes to clean and restart the board line, but if the paper break happened because of a damaged or faulty mixer part, it could take hours to get it up and running again.
Paper breaks are also expensive. Depending on the speed they run, some plants see losses in the thousands every time they shut down.
Mixing with precision
Paper breaks are essentially a failure of the slurry mix, and the resulting spill can range from an annoyance to a full-on disaster. The makeup of gypsum slurry is a simple mix of plaster (calcium sulphate hemihydrate) with water, plus binders or admixtures. As the plaster dissolves, gypsum precipitates out and forms a network of interlinked crystals with mechanical properties.
The process of mixing and setting gypsum wallboard slurry takes precise timing, moisture levels, temperature and blending. The slurry itself should be blended evenly for a smooth, homogenous mixture.
Any miscalculation can lead to costly mistakes. When handled incorrectly, gypsum naturally hardens into a cement-like substance that cakes up inside the mixer.
Common causes of paper breaks
Paper breaks often happen when the slurry forms lumps of gypsum in the mixer or boot. If you’re not careful, lumps can also solidify at the forming plate.
Poor paper or material preparation may also lead to paper breaks, specifically from cuts or tears in the edge of the paper coming off the roll.
Then there are issues with rollers. When bend rollers are too small in diameter, they can break the material fibers and cause paper breaks. The same can happen when splicing tape or glue accumulate on the rollers, or when the edges are worn.
Other mechanical issues might include problems with tensioning equipment and the forming station.
Paper break prevention
Assuming you’ve got the timing and other factors down pat, there are a few ways to prevent paper breaks in your facility. As mentioned above, it’s important to ensure your rollers and other equipment are in good shape.
We see many customers making mold-resistant products using fiberglass material instead of paper. These types of materials do not feed mold like paper.
But regular maintenance is the best preventative measure against paper breaks. A high-quality mixer and boots ensure your mix is always well-blended, and a consistent maintenance schedule keeps the mixer running smoothly for a longer period of time.
The right mixer for the right mix
We’ve been in the gypsum industry long enough to know that you can’t afford to clean up one paper break after another. Contact us to book a consultation for your facility, set up a rebuild schedule or get more information about our mixers. We’re here to help!