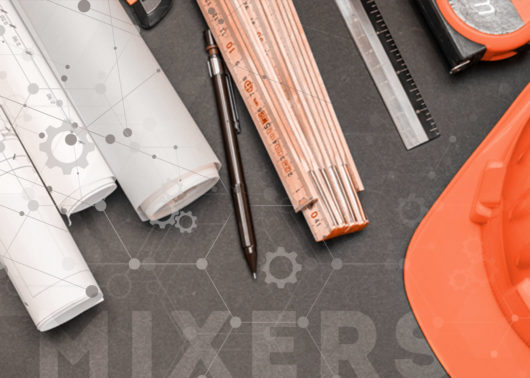
Each gypsum mixer is a little bit different. They may share many parts in common — rotors, pins, drive packages — but wallboard manufacturers put their own spin on each design, a kind of secret sauce that creates their unique brand of slurry.
A mixer engineer’s job is to take your specifications — whether it’s a CAD file or a hand-drawn design — and turn them into a working machine that does the job exactly the way you need it to.
That’s what Jim Grimes, Mechanical Designer at ACS Mixers, does best. If you gave him a napkin with a crayon sketch of your ideal mixer, Grimes could turn it into a detailed 3D drawing that actually works. (Though we prefer not to work with crayons.)
Expertise in making parts fit
Grimes spent most of his early career working in the automotive industry, where he built rotors, drums and other aftermarket brake components for more than 17 years. He later got into building exhaust and stacks for gas turbines, which he did for around 8 years.
Starting with ACS Mixers more than two years ago, Grimes now builds gypsum pin mixers for drywall companies all over the world.
His many years of experience with custom machinery in the automotive industry fits right into Grimes’ work with mixers. It’s all about paying close attention to detail to ensure parts fit together properly.
Using a meticulous, step-by-step approach, Grimes uses his extensive knowledge of mixer parts to deliver the highest possible accuracy on every mixer drawing.
Drawing out the details
While most gypsum mixers have the same basic construction, each customer’s machine has its own intricacies. Whether it’s a different lid configuration, gate sizing, or added water jets, these small alterations can help each brand make its own unique drywall slurry to differentiate in a competitive market.
When it comes to new mixers, each design exercise starts with a conversation. The ACS Mixers team gets to know more about the customer’s needs, their facility and how they want their new mixer to be configured. Then we’ll have them send a drawing with their specifications.
Grimes can take any kind of drawing, find the design flaws and fix them. He’ll go through it step by step to identify any potential issues and transform it into a mixer that works efficiently. Even sketches with measurements and requests written by hand — Grimes will turn them into a proper, working CAD file.
He works closely with our resident gypsum consultant, Wayne Beveridge, to double-check everything and ensure the parts all fit. We will sometimes consult with the customer during this process to advise them on any points of improvement.
The finishing touches
Once Grimes finishes the full package of CAD drawings, the customer can review them to confirm measurements and make any changes. Because he’s so adept at SolidWorks, the customer can physically see the modeled mixer and all of its parts before production starts, which is a huge asset to the customer and the overall timeline.
On approval, the Mixers team purchases the raw materials and starts machining all the different components. ACS invests a lot into its CNC machines, which are excellent at creating consistent parts with highly precise patterns and measurements.
Then comes assembly, QA and shipping. With all the time spent getting the drawings exactly right, customers can expect a gypsum mixer that fits their system, runs without issues, and produces a quality lump-free slurry.
Ask a mixers expert
Are you looking for a gypsum mixer engineer to turn your drawings and specs into a working mixer? Contact ACS Mixers to get started — we’ll work closely with you at every step to make sure the results are perfect for your process.