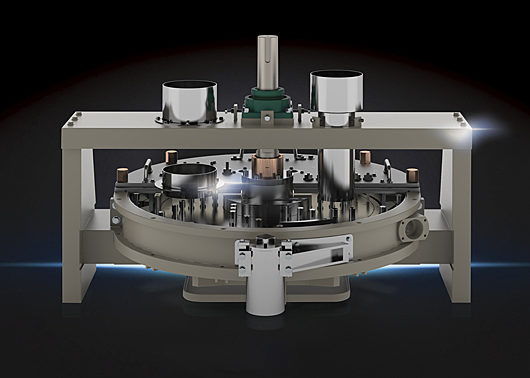
Megan Thompson, President and COO of ACS, describes the pin mixer as the beating heart of any gypsum plant.
“The mixer is the central point where everything in the plant comes together,” Thompson says. “It’s a sophisticated piece of equipment.”
That’s why it’s so important to properly build a mixer from the get-go. When the heart of the plant, the mixer, doesn’t function properly, it won’t pump out high-quality gypsum slurry.
Between Thompson, her brother and co-President/COO Greg Thompson, and Gypsum Sales and Consulting Manager Wayne Beveridge, the leaders of ACS Mixers have more than 100 years of experience in materials processing. Beveridge alone has been in the gypsum business for more than 40 years, making him the go-to consultant for many gypsum wallboard manufacturers located throughout North America.
All that knowledge and expertise goes into making the best quality mixers, boots and parts you can get. But it’s not just about the machine – the ACS team also channels a lot of effort into providing people with custom solutions, a seamless process and outstanding customer care.
So, what exactly can we do for our customers? Here’s an overview.
The parts always fit
Before they find ACS, sizing is one of the most common issues gypsum manufacturers have with their mixer’s spare parts.
“When mixers are not correct, people can spend a lot of downtime trying to make them fit,” Beveridge says. “They try to make alterations that end up damaging the chrome, or they need to put old parts back in while they send new parts back for replacement.”
That’s why, if you’re new to ACS and want to order a new mixer, we go through several steps to ensure you get the perfect drop-in replacement.
The first step is an optional site visit. We arrange to visit your plant in person to see how your process works, take measurements, and snap some specific photos for reference.
If an in-person tour isn’t possible, we can make other arrangements to get the measurements just right. We can advise you on how to get the best measurements, arrange for you to send us some key pieces, or transport your old mixer for evaluation.
After we get the right measurements, we’ll send you an initial set of drawings to sketch out the basics. On approval, you send a purchase order (PO), and our engineering department gets started on a full package of detailed drawings. Any changes we need will be confirmed as build drawings.
“Everything is done digitally,” Beveridge explains, adding that the drawing stage is critical to ensure accurate sizing. “We have a library of drawings, templates and sometimes 3D models for every mixer we’ve sold.”
Once those drawings are approved, we start the build.
As you can see, we’re adamant that everything gets double-checked and verified before we move on to the next step. If there’s anything that may make it difficult for the mixer to line up, we can correct it in our designs before the build begins.
In other words, if you need a drop-in replacement mixer, Beveridge and his team will make sure you get an exact fit.
“Our parts always fit. We pretty much guarantee it,” he says.
No two mixers are the same…
Every mixer is different, which is why that site visit is such an important first step. We can take a look at the unique features of your plant or understand any custom alterations on your old mixer. If you’re concerned about any proprietary features on the mixer, it’s common for us to sign a non-disclosure agreement (NDA) to keep everything strictly confidential.
We provide both imperial and metric-fitted mixers, as our customers in Europe usually require mixers with bolts, nuts, fasteners and pipe fittings sized for the metric system.
Requests are usually specific to the customer. Beveridge personally handles many questions about mixer maintenance, installation or dismantling, operation, parts replacements, and all kinds of troubleshooting issues.
“Whatever issues customers need help with, I’m here to be that resource, because I’ve dealt with those same problems in my career,” he says.
If you’re looking for the smoothest possible experience with your new mixer, there’s no substitute for decades of expertise. The ACS Mixers teams put plenty of care and attention into every single order.
“We do all the documentation. We take all the steps to make sure everything is exactly the same,” Beveridge says. “We can make a 3D model from a 2D drawing in a matter of hours, make design changes in minutes, and help people out when they have a problem.”
If you’re new to ACS and are having issues with another mixer, it may be more cost-effective to buy a new model from a more reliable manufacturer. ACS also offers mixer repair and rebuilding services to help extend the lifespan before you need to buy another new model.
Not sure exactly what you need? We can help with that, too. Give ACS a call for answers to all your mixer-related questions.