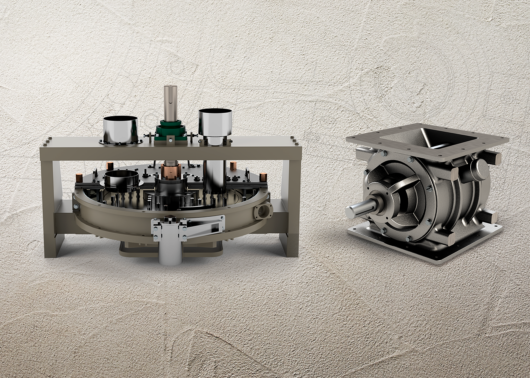
In a gypsum processing plant, the pin mixer has a central role. It’s where the magic of mixing slurry happens, and the quality of your end product ultimately depends on the mixer’s performance.
Rotary airlock valves also play a critical role, but in a much different way. One gypsum plant could have hundreds of rotary valves, which are used most commonly for dust collectors.
How are valves used for dust collectors?
No matter how you move gypsum, it creates a lot of dust. If left unchecked, dust particles can escape into the plant environment, wasting material and creating a health hazard for workers.
Dust collectors are installed at every step to capture stray particles and return them to the process, allowing them to be reused. To prevent leakage between containers, the rotary valves attached to these dust collectors must create a pressurized seal. They must also meter out material at a specific rate, usually based on weight, with special parameters for that particular slurry recipe.
What kind of valve can do the job?
For rotary valves in the gypsum industry, accuracy and reliability are a must. You don’t want valves that will cause issues requiring you to shut down the line for troubleshooting. They also need to be tough. Gypsum is a moderately abrasive ingredient, but other additives, such as vermiculite, can wear down equipment even faster.
We generally recommend a CI Series rotary valve for this application. The square-flange CI – along with its round-flange counterpart, the MD Series valve – is a highly customizable base that can be equipped with the right features and options for gypsum processing.
What are the right features?
This can vary depending on the location of the rotary valve and its purpose in your plant, but we can make a few general suggestions.
The first is an air purge kit. There are two kinds that use compressed air to blow dust in the right direction. Shaft seal purge assemblies keep material away from the shaft seal and bearings area of the rotary valve, which prevents the material from wearing down those components.
Similarly, rotor pocket purge kits prevent material build-up inside the rotor pockets. For gypsum, you should use a combination of the two.
Beyond that, a hard chrome coating will protect your valve from general wear-and-tear. The rotor will need to be replaced regularly, but an AR 400 plate coating will extend the maintenance cycle. We sometimes recommend a vent port to release pressurized air as needed.
The right configuration will reduce maintenance, extend longevity, and make your rotary valve set-up much more cost-effective. In a plant with dozens or hundreds of valves, the savings can really add up.
How do I learn more about valves for gypsum?
You can find specifications, 3D images, and details about rotary valves for gypsum plants on our website.
To place an order or learn more about our customization options, get in touch with an ACS Mixers representative. We’re always happy to help.