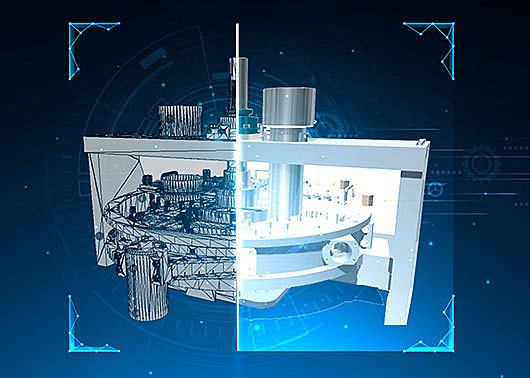
Like snowflakes and fingerprints, no two gypsum pin mixers are the same.
That’s because everyone’s drywall manufacturing process is a little bit different. To stay competitive in the industry, everyone uses different ingredients, additives, and equipment to make a slurry that stands out from the rest.
Gypsum pin mixers have some basic components in common, but we never sell them off-the-shelf. Everything needs to be properly sized, and sometimes parts are custom-built to your specifications.
Mixers: The framework
At its most basic, a gypsum pin mixer is made up of a base, frame, and lids. The dimensions are pretty much always the same, but they get taller for larger mixers for higher capacity.
The 3D mixer models on our website have that same basic design, with no drive components or unique features. If you need a special part, they are custom-built or sometimes handmade to ensure it fits perfectly with the specific design of your system.
When do I need a custom component?
Often, our customers have set requirements for a custom component — a kind of “secret sauce” that is unique to their process of making drywall slurry.
One common example is oversized parts. The standard diameter for lid pins is 1/2’’, but sometimes our customers prefer to increase the diameter of the stationary pins (lid pins and water pins). We can increase the size up to 5/8’’ to close the gap between the rotor pins and lid pins. By tightening up the space that the slurry can slip through, some customers will notice better mixing as the molecules get stirred up more thoroughly, forming fewer lumps and making better stucco as a result.
If you’re not sure, you can also come to ACS Mixers for recommendations. Whether you have a common problem in production, you’re faced with a slurry anomaly, or you just need to improve efficiency, our veteran mixer consultants can suggest a solution.
What goes into custom-made components?
First, we take our customer’s description of the problem, their ideal solution, and any drawings they may have. Then we design the solution to make sure it works well with the mixer.
The customer gets a set of technical drawings to review before any production starts. We sometimes create a model to make sure it matches up with what they envisioned.
Once the order is approved, we’ll create a computerized laser cut or CNC part to make the next one smooth and painless. Your drawings and part numbers are always documented and kept on file, so you can easily re-order what you need.
An example of a custom solution
One particular plant was having trouble with buildup inside the extraction port of their mixer. Because of the way their system was set up, the material would block off the port in certain areas and clog it up. The problem was bad enough that they often had to shut down just to clean out the buildup on that one part.
So, they asked us to shrink down the design of the extraction port. We worked with them to ensure the part was the right size to get the result they wanted. By shrinking the design, they shortened the distance it took for material to move through the device, which helped the material move through quickly without build-up.
Since then, the change has helped prevent blockages, and they shut down the plant less often as a result. Because we have the templates on hand, we’re able to supply them with the same custom-designed part each time they need a new part.
Stay one step ahead
At the time of writing, supply chains are still shaky, so it’s important to stock up on the right parts in advance of any problems. To learn more, check out our other blog about the importance of keeping spare parts on hand — especially if they’re custom-made.
We have lots more to share about the technical aspects of gypsum pin mixers, but if you have a specific problem, call the experts at ACS Mixers. We’ll help you come up with the solution that works best for your process.