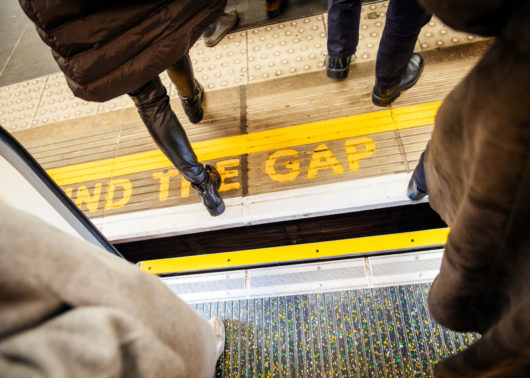
Lest there be a gap in your knowledge, let’s be clear about something: you must check your rotor-to-housing tolerances, or clearances, on a regular basis.
It’s something we write about so often we sound like broken records. But we’re happy to keep singing the same old tune, because we want our customers to get the best possible longevity, efficiency and value out of their rotary airlock valves.
Mind the gap
Need a quick breakdown? The rotor-to-housing tolerance is a measurement of the space between the rotor tips and valve housing. Rotor tips wear down over time — that’s a normal part of the process, though it happens faster with abrasive material.
That sandpaper effect gradually enlarges the space between the tips and the housing. If you don’t do anything about it, air will sneak through the gaps, and your valve won’t work properly as an airlock.
Get the right flow rate
“When you monitor your rotor clearances, your whole system runs better and conveys the material rate you require,” says Megan Thompson, President and COO of ACS Valves. “Worn-out rotor tips won’t convey the right amount of material.”
Let’s say, for example, that your ideal output is a rate of about 10,000 pounds of material per hour. With decreased clearances, you might only get 8,000 pounds per hour.
That’s because there’s too much air coming up on the return side of the valve, which prevents the pockets from filling up with the right amount of material.
“Basically, the valve becomes inefficient over time — it’s not doing its job,” Thompson explains.
Stay NFPA compliant
As we covered above, a rotary valve can’t do its job as an airlock if the clearances are too large. That’s a concern in terms of fire safety and NFPA compliance.
In the event of a fire in your conveying line or dust collector, the rotary airlock valve works as an isolation device. It cuts off the oxygen sources and stops the spread of flames. According to NFPA-69, clearances must stay under 0.0079’’ to work effectively as isolation devices.
Control the maintenance process
We recommend checking your tolerances every three months on a historical maintenance schedule. If they seem consistently intact after a few three-month intervals, you can try scaling back to every four or five months and see if that is a more efficient schedule.
Without a solid schedule, you risk having to shut down your system at an inopportune time to replace the rotor and deal with any other complications.
“If you monitor the clearances, you get to dictate when you’re going to take out that rotor and put a new one in,” Thompson says. “You could make it coincide with a day of planned downtime.”
She also recommends looking at rotors made from different types of steel, depending on your application and the material being conveyed. Some materials do better with a stainless-steel construction rotor, while other more abrasive applications like cement powder work best with harder types of steel, such as AR400 steel.
In the clear
Ready to get started? Check out our short-and-sweet video guide on how to measure rotor-to-housing tolerances. If you have other questions, we’re always here to help.